sensXPERT is closing its doors.
We would like to inform you that we have concluded our business operations effective July 31, 2025.
This decision was not made lightly, and it marks the conclusion of an important chapter for us. We are deeply grateful for the interest, engagement, and support we have received over the years. It has been a meaningful journey, and we sincerely thank everyone who has been part of it in any way.
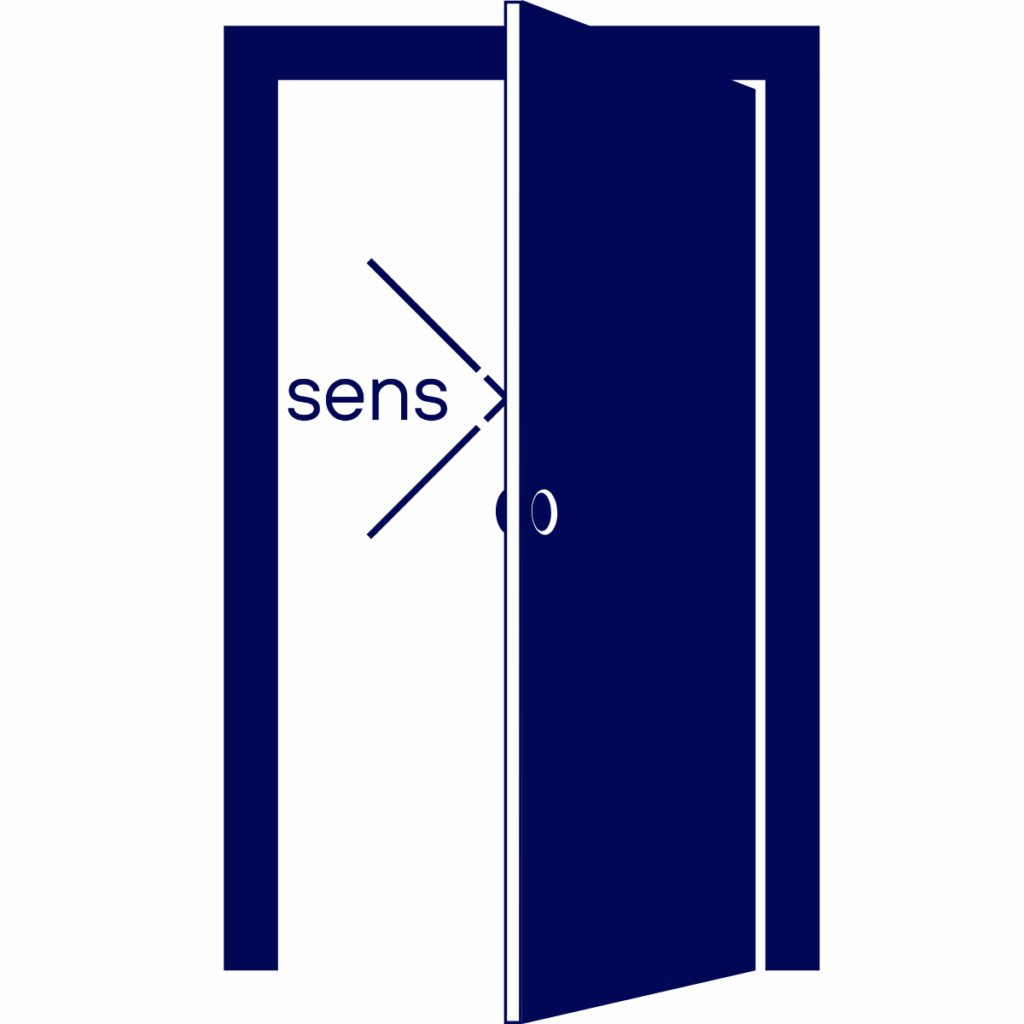