Process optimization thermosets: How to solve the challenges of the future
Political demands for more sustainable manufacturing processes are a major challenge. In addition to the associated risks, there are great opportunities for companies that are open to these changes.
In the world of thermosets, process optimization is key to meeting these challenges. In this article, you will learn how you as a thermoset processor, but also as a thermoset manufacturer, can optimize your processes and make them more sustainable in the future. So be sure to read on.
Thermoset process optimization: How to solve the challenges of the future
More sustainable products, shorter production cycles, material shortages, skills shortages, new regulatory requirements (e.g. the new EU taxonomy) as well as lower scrap rates and high-quality standards: The plastics industry is currently under high pressure to rethink and innovate traditional manufacturing with thermosets (and thermoplastics).

Stricter regulations are forcing the plastics industry to act
New legislation, such as the EU taxonomy, no longer leaves much room for maneuvering. Especially companies that depend on investment funds are “forced” to act by the new legislation.
Conclusion: In order to meet the requirements in Europe and at the same time remain competitive, the plastics industry must develop new processes and use intelligent technologies. So how can small and medium-sized companies respond effectively to these challenges? In the next sections, we will show you approaches to solutions on how you can best equip your production for Industry 4.0.
Process optimization for thermosets: What are the levers?
As you already know, the thermoset industry has a number of challenges to overcome in the future. Using smart software and innovative tools can equip you with the tools you need to navigate the big opportunities of change well (and profitably). Find out how to innovate your existing thermoset processing and which set screws you can use with sensXPERT in the further article.
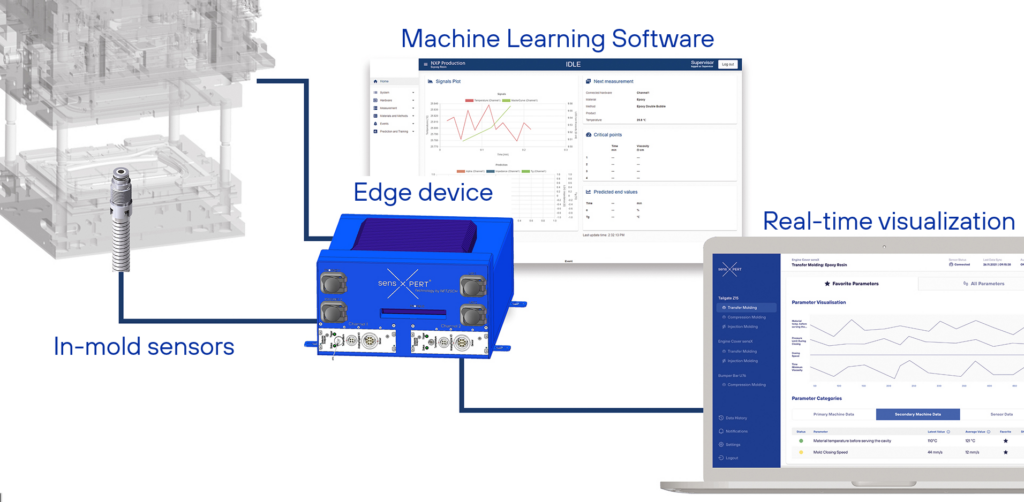
Adaptation and optimization of manufacturing processes
The holistic optimization of your manufacturing process is sensXPERT’s top priority.
Through the interaction of two components – tool sensors and AI software with machine learning capabilities – sensXPERT prepares your production for Industry 4.0. The fully integrated tool sensors send important input, such as information about material behavior or temperatures during production, to the software.
The cooperation of the sensor technology with the software enables your complete manufacturing process to be transparent, giving you insights into important quality characteristics, such as
- the degree of curing,
- the machine pressure,
- the viscosity of the material
- and other production metrics.
The software combines mathematical and physicochemical models of polymer behavior with machine learning algorithms. In a second step, this raw data is translated into predictive quality criteria that allow you to make qualitative statements about the quality of individual parts as well as to adjust deviating production parameters.
Concrete advantages of using sensXPERT
Reduce scrap rates/ optimize quality control
Improving production and reducing scrap rates using new technologies is only possible with the help of a solid database from materials science – in this case: important parameters such as the degree of curing or the glass transition temperature.
sensXpert not only takes into account the fundamentals of materials science in its simulation models but also combines them with reaction kinetics. This gives you a clear and complete picture of the state of the thermoset material during and after production.
You can use this information specifically for your internal quality control to control your production and reduce the reject rate.
Compensate for the shortage of skilled workers/ Provide employees with helpful tools
The cloud-based system gives the attending technician vital information that helps them effectively monitor a specific production line in a focused manner. As soon as the sensXPERT software identifies patterns in a data set as deviating, the technician on site is alerted. Now he has the opportunity to intervene in production and correct deviations and prevent rejects.
The interaction of the sensors and AI software and the resulting real-time data gives you a complete and valuable picture of the current production cycle at any point in production.
Increase productivity by up to 30%
By analyzing the material behavior and its properties in real-time during production, you get the opportunity to continuously increase your productivity. And that by up to 30%!
Provide sustainability data for future reporting requirements
The new EU taxonomy, which will soon affect all SMEs in the plastics industry, will require the provision of sustainability data for your production in the future, should you wish to continue to have cost-effective access to the financial market.
sensXPERT enables you to provide sustainability data for each molded part at any time, thanks to the transparency and information gained about your production. So you know, in black and white, what the inner workings of the finished product “look like” in each of the parts produced, and you can satisfy the reporting requirements of lenders.
Reduce processing costs, energy consumption and waste.
Once your scrap rates are reduced, you will logically need less energy and raw material to achieve the same results as your production. So, thanks to sensXPERT, optimizing your production will also translate into a reduction in energy consumption and processing costs.
Conclusion: With this combination of current process data and basic information about the thermoset material you are using, you can avoid errors, provide targeted support for production staff and – quite incidentally – meet sustainability requirements.
In the world of thermosets, process optimization is the key to mastering these challenges. If you, as a manufacturer of thermosets, want to optimize your processes and make them more sustainable in the future, sensXPERT should not be missing from your operation. If you have further questions about the implementation of process optimization in your company, do not hesitate to call us.