Wie ein führendes Luftfahrtunternehmen ihre Flugzeugproduktion mit sensXPERT transformierte
Wichtigste Fakten

Der Druck des Marktes belastet die Hersteller von Luft- und Raumfahrtteilen zunehmend, insbesondere im Hinblick auf Industrie 4.0. Um den aktuellen Anforderungen gerecht zu werden, hat ein führendes Unternehmen der Luftfahrtindustrie mit sensXPERT zusammengearbeitet, mit dem Ziel, die Effizienz zu steigern.
Das Luftfahrtunternehmen stellt faserverstärkte Verbundteile her, die für die Unterstützung des Rumpfes verwendet werden. Da es sich um ein großes und komplexes Teil handelt, besteht der langwierige Produktionsprozess aus mehreren Schritten. VARTM, Abkühlphasen und Aushärtung im Autoklaven, um genau zu sein.
Durch die Implementierung von sensXPERT und die Digitalisierung des Prozesses erhielt das Luftfahrtunternehmen Einblicke in die Leistungsprognosen des Bauteils, was Korrekturen vor den nachgelagerten Qualitätssicherungsprüfungen ermöglichte. Es wurden nur 50 Minuten an Messdaten benötigt, um das Ergebnis eines Zyklus vorherzusagen und entsprechend zu optimieren. Die Steigerung der Prozesseffizienz ist nur einer der Vorteile, die die Digitalisierung in diesem Fall mit sich brachte.
Die Luftfahrtindustrie ist ein sich stetig weiterentwickelnder Sektor, geprägt von Innovation. Seit der erfolgreichen Erfindung des schwerer-als-Luft-Flugzeugs durch die Gebrüder Wright haben Wettbewerb und der Drang nach Fortschritt die Branche zu einem Vorreiter im wissenschaftlichen und technologischen Fortschritt gemacht.
Dieser Fortschritt lässt sich eindrucksvoll durch die Expansion der Branche veranschaulichen: Die globale Flotte soll von 24.510 Verkehrsflugzeugen im Jahr 2023 auf beeindruckende 48.575 im Jahr 2042 anwachsen.

Während diese Zahlen die Größe der Branche verdeutlichen, ist ein wesentlicher Faktor für das erwartete Wachstum der groß angelegte Produktionshochlauf, den Luftfahrt-OEMs planen, um ihre überfüllten Auftragsbücher abzuarbeiten. Dieser Hochlauf wird durch die Bemühungen der Fluggesellschaften angetrieben, die gestiegene Verbrauchernachfrage nach der Pandemie zu befriedigen und effizientere Flugzeugmodelle in ihre Flotten zu integrieren.
Allerdings hat sich der Luftverkehr seit COVID-19 schneller erholt als die Flugzeugproduktion, was den Druck auf die Hersteller erhöht hat. Sie müssen die Produktion steigern und gleichzeitig sicherstellen, dass jede Komponente höchsten Qualitäts- und Sicherheitsstandards entspricht. Zusätzlich liegt der Fokus der Branche zunehmend auf der Erreichung von Nachhaltigkeitszielen. Während der CO₂-Fußabdruck ein wichtiger Indikator ist, stehen KPIs im Vordergrund, die den Energieverbrauch senken und Rohstoffe effizient nutzen, um Ausschuss zu vermeiden. Mit der Einführung neuer Verarbeitungstechnologien und Software wird die Nutzung von Daten zu einem wesentlichen und entscheidenden Bestandteil der Nachhaltigkeitsbemühungen. Einfache Maßnahmen wie die Echtzeitüberwachung der Aushärtung und das Verständnis des Materialverhaltens während der Verarbeitung helfen der Branche, informiert und auf dem neuesten Stand der Trends zu bleiben. In diesem anspruchsvollen Umfeld ist Effizienz der Schlüssel.
Leider erweist sich die Steigerung der Produktionseffizienz in einer Branche, die strengen Vorschriften und Qualitätsstandards unterliegt, als Herausforderung. Um die strengen Sicherheitsanforderungen zu erfüllen, verlassen sich Hersteller häufig auf traditionelle Prozesse wie die Aushärtung im Autoklaven, die lange Sicherheitsreserven im Zyklus beinhalten, um eine vollständige Aushärtung der Komponenten zu gewährleisten. Diese langen Zykluszeiten, der hohe Energieverbrauch und der geringere Durchsatz behindern jedoch eine effiziente Fertigung und erschweren das Ziel, die Produktion hochzufahren.
Das führende Luftfahrtunternehmen in dieser Fallstudie war stets Vorreiter bei Fortschritten in der Luftfahrtproduktion. Daher wandte sich das Unternehmen 2016 im Rahmen seines kontinuierlichen Strebens nach Innovation, Produktionsoptimierung und effizienter Fertigung an NETZSCH Analyzing & Testing, um die Möglichkeit einer Inline-Materialcharakterisierung zu untersuchen.
Was als einfache Anfrage zur Verbesserung der Produktionsüberwachung begann, entwickelte sich unerwartet zu einer wegweisenden Zusammenarbeit, die die Grenzen der Luftfahrtfertigung verschob.
Dies ist die Geschichte, wie ein führender Hersteller in der Luftfahrtindustrie die sensXPERT Digital Mold-Lösung integrierte, Echtzeit-Aushärtungsüberwachung und Prozesskontrolle nutzte, um seine Prozesse zu revolutionieren, Zykluszeiten drastisch zu verkürzen und eine tadellose Komponentenqualität sicherzustellen. Damit setzt das Luftfahrtunternehmen neue Maßstäbe in der Branche.
Der Fertigungsprozess des Unternehmens
Bei der Herstellung tragender Flugzeugkomponenten setzt der Luftfahrthersteller fortschrittliche Techniken und Hochleistungsmaterialien ein, um die höchsten Standards in Qualität und Sicherheit zu gewährleisten.
Der Prozess beginnt mit der Auswahl von Verbundwerkstoffen, hauptsächlich kohlenstofffaserverstärkten Polymeren (CFRP), die sich durch ihr herausragendes Verhältnis von Festigkeit zu Gewicht und ihre Haltbarkeit auszeichnen. Die ausgewählten Carbonfasern werden zu Geweben verarbeitet und anschließend mit RTM6-1, einem Epoxidharz in Luft- und Raumfahrtqualität, bekannt als Hex Flow® von Hexcel Corp., vorimprägniert. Diese Kombination bildet die Prepreg-Materialien, die für die strukturelle Integrität der Bauteile entscheidend sind.
Der Fertigungsprozess zeichnet sich durch den präzisen Einsatz des vakuumunterstützten Harzinjektionsverfahrens (VARTM) und die anschließende Aushärtung im Autoklaven aus. Während des VARTM werden trockene Faserpräformen exakt zugeschnitten und manuell in eine spezielle Form eingelegt. Diese wird anschließend versiegelt, und ein Gemisch aus Epoxidharz und Härter wird unter Vakuum injiziert. Dieser Prozess dauert typischerweise bis zu 150 Minuten und beinhaltet eine langsame Aushärtung bei niedrigen Temperaturen, um Verformungen und Spannungen zu vermeiden. In diesem Verfahren strebt der Hersteller einen Aushärtungsgrad (Degree of Cure, DoC) von 80 % an, der für die vorläufigen strukturellen Eigenschaften des Bauteils entscheidend ist.
Nach dem VARTM-Verfahren durchlaufen die Teile eine wichtige Abkühlphase, bei der die Temperatur schrittweise von etwa 150 °C auf eine Entformungstemperatur von etwa 50 °C gesenkt wird. Diese Phase ermöglicht es den Bauteilen, auszuhärten und einen DoC von mindestens 80 % zu erreichen, bevor sie aus der Form entnommen werden.
Der letzte Schritt umfasst die Aushärtung im Autoklaven, eine besonders wichtige Phase. Dabei werden die Teile kontrollierten Druck- und Temperaturzyklen ausgesetzt, um ein sekundäres DoC-Ziel von etwa 95 % zu erreichen. Dieser Schritt ist entscheidend, um die mechanischen Eigenschaften des Bauteils abzuschließen und eine langfristige Leistungsfähigkeit sicherzustellen.
Das Luftfahrtunternehmen hält stets strenge Standards ein, um die Qualität und Sicherheit jedes einzelnen Bauteils zu gewährleisten. Um an der Spitze der Branche zu bleiben, sucht es kontinuierlich nach Möglichkeiten, seine Produktionsprozesse zu optimieren, indem es jeden Aspekt genau analysiert, um potenzielle Effizienzsteigerungen zu identifizieren.
Erkennung von Ineffizienzen
Im Rahmen ihres Engagements für kontinuierliche Verbesserung identifizierte der Luftfahrthersteller einige zentrale Optimierungsmöglichkeiten in seinem Fertigungsprozess, die greifbare Effizienzsteigerungen versprachen.
Eine der Hauptineffizienzen im Herstellungsprozess sind die langen Zykluszeiten und Sicherheitsreserven, die für die ausreichende Aushärtung von Verbundwerkstoffkomponenten erforderlich sind. Obwohl diese verlängerten Zeiten notwendig sind, um die angestrebten Aushärtungsgrade (DoC) zu erreichen, wirken sie sich erheblich auf den Energieverbrauch und die Produktionskosten aus.
Zudem führen geschlossene Formprozesse zu einem Mangel an Transparenz hinsichtlich des Echtzeit-Materialverhaltens, was die Bestimmung optimaler Zykluszeiten für das Entformen erschwert. Dies resultiert häufig in konservativen Schätzungen, die den Prozess verlängern.
Darüber hinaus, obwohl der Hersteller in seinen etablierten Prozessen erfolgreich ist, wird das Umfeld, in dem er tätig ist, sowohl von internen Abläufen als auch von externen regulatorischen Rahmenbedingungen geprägt.
Navigieren durch regulatorische Standards: EASA
Eine der zentralen Regulierungsbehörden, die die Branche beeinflussen, ist die Europäische Agentur für Flugsicherheit (EASA). Die Vorschriften der EASA sind maßgeblich für die Festlegung von Sicherheitsstandards und Compliance-Anforderungen, die die Betriebs- und Produktionsstrategien von Luftfahrtherstellern direkt beeinflussen.
Im Bestreben, die strengen Standards der EASA zu erfüllen, müssen Luftfahrthersteller deren Vorschriften einhalten, wenn sie neue Prozesse einführen oder bestehende mit neuer Technologie verbessern. Das Mandat der EASA umfasst die gesamte Herstellung und Wartung von Flugzeugteilen, von Triebwerken bis hin zu Avionik- und Strukturkomponenten. Jedes Teil muss zertifiziert werden, um spezifische Sicherheitsstandards zu erfüllen. Dieser Prozess umfasst eine umfassende Dokumentation, um die Historie des Bauteils bis hin zum Hersteller zurückzuverfolgen. Dieser aufwendige Prozess stellt die Authentizität und Integrität jedes Bauteils sicher und unterstreicht das Engagement der EASA für Sicherheit und Qualität.
Darüber hinaus regelt die EASA-Part-21-Verordnung ausdrücklich die Herstellung von Flugzeugteilen und legt detaillierte Anforderungen an Designprüfung, Produktionsmethoden und Qualitätssicherung fest.
Hintergrund der Lösung: Optimierung des Fertigungsprozesses
Im Jahr 2016, angesichts der Herausforderung, die strengen EASA-Standards einzuhalten und gleichzeitig die Produktionseffizienz zu verbessern, ergriff der Luftfahrtmarktführer proaktiv Maßnahmen. Das Unternehmen initiierte eine Zusammenarbeit mit NETZSCH Analyzing & Testing, um die Inline-Materialcharakterisierung zu nutzen und den Aushärtungsprozess seiner Verbundwerkstoffkomponenten zu optimieren. Der erste Schritt dieser Partnerschaft war die Installation eines Systems zur dielektrischen Analyse (DEA) in einem der Autoklavprozesse des Herstellers. Diese frühe Installation war entscheidend, um Echtzeitdaten zu Materialparametern wie DoC (Degree of Cure), Temperatur und Viskosität während des Aushärtungsprozesses zu liefern – Parameter, die für die Produktion hochwertiger und sicherer Komponenten gemäß den EASA-Vorgaben unverzichtbar sind.
Zwischen 2016 und 2020 verfeinerte das Team von NETZSCH Analyzing & Testing die DEA-Technologie weiter. Das Hauptziel bestand darin, sicherzustellen, dass das Überwachungssystem präzise und zuverlässige Daten lieferte und diese mit den Qualitätsstandards der Luftfahrtindustrie in Einklang brachte.
Im Jahr 2021 unternahm NETZSCH einen bedeutenden Schritt und gründete die NETZSCH Process Intelligence GmbH (sensXPERT). Dieses neue Unternehmen widmet sich der Weiterentwicklung der Prozessüberwachung und führte zur Entwicklung der sensXPERT Digital Mold Solution. Das System wurde speziell entwickelt, um eine umfassende Materialcharakterisierung direkt in der Form zu ermöglichen und dabei verschiedenen Druck- und Temperaturanforderungen standzuhalten. Es eignet sich für Verfahren wie Reaction Injection Molding, VARTM und Autoklav-Aushärtung und demonstriert so seine Vielseitigkeit.
Nach der Integration der sensXPERT Digital Mold Solution in seinen VARTM-Prozess konnte der Luftfahrthersteller umfangreiche Einblicke in Formprozesse und Materialeigenschaften gewinnen, darunter DoC, Polymerisationsgrad, Glasübergangstemperatur (Tg) und Viskosität. Die Fähigkeit der sensXPERT-Lösung, Echtzeitdaten zu erfassen und Materialeigenschaften zu charakterisieren, erfüllt die Qualitätskriterien sowohl des Luftfahrtunternehmens als auch von Organisationen wie der EASA.
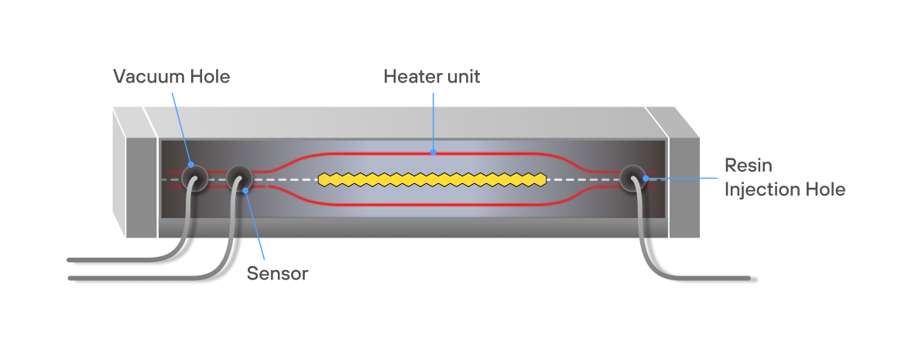
Durch die Echtzeit-Materialcharakterisierung direkt in der Form während des VARTM-Prozesses ermöglichte diese fortschrittliche Überwachungslösung eine präzise Kontrolle des Aushärtungsprozesses. Sie erlaubte automatisierte Anpassungen, die die Zykluszeiten beim optimalen Aushärtungsgrad (80 % DoC) stoppten. Diese Optimierung war entscheidend, um hochwertige Ergebnisse zu erzielen und gleichzeitig die Effizienz erheblich zu steigern.
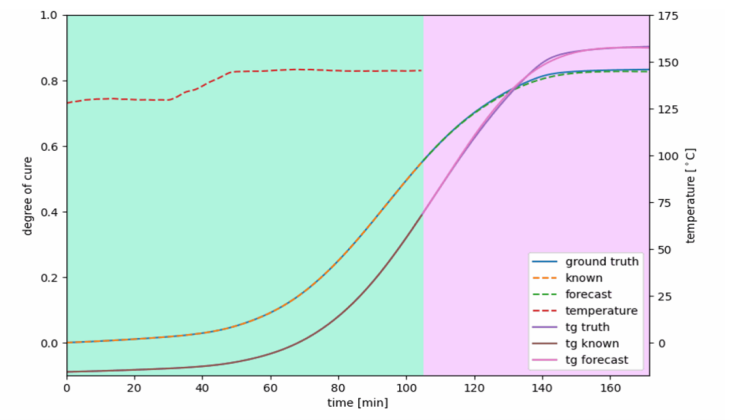
Eines der bemerkenswertesten Ergebnisse der Lösung war die Verkürzung der Zykluszeiten. Durch die präzise Identifizierung des optimalen Aushärtungsgrads konnte das Luftfahrtunternehmen die Dauer des VARTM-Zyklus durchschnittlich um 13 % ± 5,3 % und maximal um 20 % reduzieren.
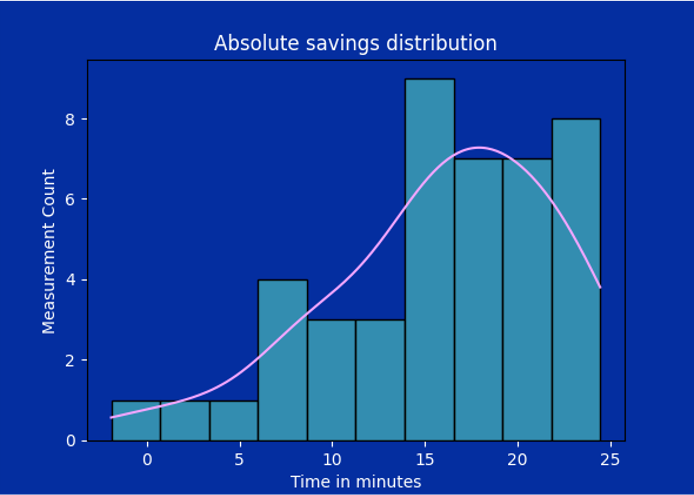
Zusätzlich ermöglichte die verbesserte Prozesstransparenz Echtzeitanpassungen, wodurch die Abhängigkeit von konservativen Sicherheitsreserven reduziert wurde. Ein weiterer bedeutender Vorteil war die gesteigerte Energieeffizienz. Durch die Minimierung der Zeit, die Komponenten im Aushärtungsprozess verbrachten, erreichte der Luftfahrthersteller eine bis zu 23% höhere Energieeffizienz, wodurch die Betriebskosten und der ökologische Fußabdruck des Fertigungsprozesses gesenkt wurden.
Die Implementierung der sensXPERT Digital Mold Solution verbesserte die Produktionsprozesse für CFRP-Komponenten des Unternehmens erheblich.
Ein erfahrener Verbundwerkstoffexperte des Luftfahrtunternehmens fasst die Fähigkeiten der sensXPERT-Technologie wie folgt zusammen:
„Die Kombination aus verkürzten Zykluszeiten, gesteigerter Energieeffizienz und verbesserter Prozesstransparenz unterstreicht den Wert von Echtzeitüberwachung und dynamischen Anpassungen, um operative Exzellenz zu erreichen. Sie ist ein unschätzbarer Beitrag zu dem, was unser Unternehmen anstrebt – die führende Position in der Luftfahrtindustrie.“
Die Zusammenarbeit zwischen diesem Luftfahrthersteller und sensXPERT ist fortlaufend und hat sich inzwischen von einer Vorproduktionsphase zur Serienfertigung weiterentwickelt.
Mit diesen Fortschritten sieht die Zukunft für alle Luftfahrthersteller vielversprechend aus, da sie Echtzeit-Prozesskontrollinnovationen übernehmen, um Effizienz, Nachhaltigkeit und Wettbewerbsfähigkeit in der Branche zu steigern.
Interessiert an weiteren Informationen?
Qualität und Effizienz in der Luftfahrt: Nutzung der dielektrischen Analyse für die Prozesskontrolle
Sehen Sie ein exklusives Interview-Webinar mit sensXPERT und Testia (einem Unternehmen von Airbus) und erfahren Sie, wie dielektrische Analyse zu einem unverzichtbaren Werkzeug für die Echtzeit-Qualitätskontrolle in der Luftfahrtfertigung wurde. Lernen Sie von Experten, wie automatisierte Datenanalysen und Prozessanpassungen Herstellern helfen, strenge Branchenstandards zu erfüllen und gleichzeitig die Effizienz zu optimieren.
Schauen Sie sich das kostenlose On-Demand-Webinar an!
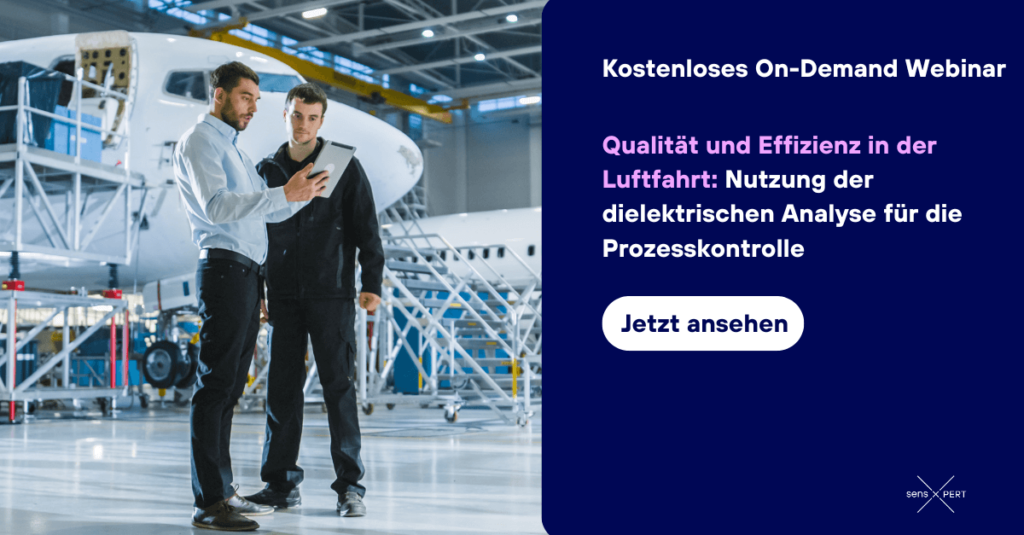