Optimierte In-situ-PA6-Polymerisation durch präzise Prozesskontrolle
Das Wichtigste Im Überblick

Qualitätssicherung und Prozesseffizienz sind entscheidend für die Einhaltung von Branchenstandards und die Steigerung der Glaubwürdigkeit.
Ein großer Kunststoffhersteller hat sensXPERT Digital Mold in ihrer in-situ Polymerisation von PA6 implementiert, um die Produktionseffizienz, die Qualitätsüberwachung und die Prozesskontrolle zu erhöhen.
Durch die Integration von sensXPERT in ihre Produktion konnte das Unternehmen die Zykluszeiten um 12,5 % verkürzen und kontinuierlich optimale Teile herstellen.
Qualitätssicherung ist in jeder Fertigungslandschaft unerlässlich, insbesondere beim Beliefern von Branchen, in denen Sicherheit und Leistung oberste Priorität haben; denken Sie an die Automobil-, Luftfahrt- und Medizinindustrie. Neben der garantierten Produktleistung und der Einhaltung von Sicherheitsanforderungen ermöglichen Qualitätssicherungsmaßnahmen Herstellern, Branchenstandards und -vorschriften zu erfüllen sowie Zertifizierungen zu erlangen, um die Glaubwürdigkeit zu stärken.
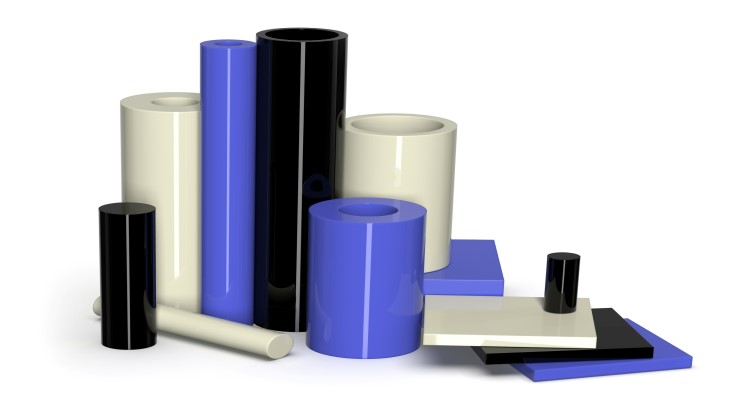
Mit Qualitätssicherung als wichtigem Antrieb für die meisten Hersteller wandte sich ein großes Kunststoffproduktionsunternehmen an sensXPERT, um ihre Prozesse zu optimieren, die Produktionseffizienz zu steigern, die Qualitätssicherung zu verbessern und eine größere Kontrolle über ihre Abläufe einzuführen.
Dieser große Kunststoffhersteller bedient zahlreiche Branchen, von der Automobil- bis zur Medizinbranche, und strebt danach, seinen Kunden Teile von höchster Qualität zu liefern. Daher sind Qualitätstests und -überwachung in jedem Stadium ihrer Produktion entscheidend – von der Beschaffung von Rohstoffen bis zum Versand der Produkte. Aus diesem Grund sucht das Unternehmen kontinuierlich nach neuen Möglichkeiten, um ihre Qualitätssicherung und Produktionsleistung voranzutreiben.
Material- und Prozess-Einblicke
Als Teil ihres Produktportfolios stellt das Unternehmen große, dicke Teile durch die In-situ-Polymerisation von PA6 her.
Polyamide 6
PA6, auch bekannt als Polyamid 6 oder Nylon 6, ist ein vielseitiges halbkristallines Thermoplast-Polymer mit einer breiten Palette von Eigenschaften, die es zu einem wertvollen Material für verschiedene Anwendungen machen. Es wird durch die Polymerisation von Caprolactam, einem cyclischen aliphatischen Amid, hergestellt. PA6 zeichnet sich durch seine außergewöhnlichen mechanischen Eigenschaften aus, darunter hohe Zugfestigkeit, Schlagfestigkeit und Verschleißfestigkeit. Es zeigt auch eine gute Ermüdungsbeständigkeit, Dimensionsstabilität und geringe Feuchtigkeitsaufnahme.
Darüber hinaus ist PA6 relativ einfach zu verarbeiten, was es zu einem kostengünstigen Material für die Massenproduktion macht. PA6 ist eine gängige Wahl für Anwendungen, die hohe mechanische Leistung erfordern, wie Zahnräder, Lager und Maschinenkomponenten. Seine gute chemische Beständigkeit macht es für Anwendungen in den Bereichen Automobil, Elektrik und Luft- und Raumfahrt geeignet.
Zusätzlich zu seinen grundlegenden Eigenschaften kann PA6 durch verschiedene Techniken modifiziert werden, um spezifische Merkmale zu verbessern, wie z. B. das Mischen mit anderen Polymeren, das Zugabe von Füllstoffen oder Verstärkungen und die Einarbeitung von Additiven. Diese Modifikationen können PA6 für spezifische Anwendungen maßschneidern, wie z. B. die Erhöhung seiner Steifigkeit, Flammschutzfähigkeit oder Temperaturbeständigkeit.
Was ist die In-situ-Polymerisation?
Die Polymerisation ist ein grundlegender Prozess in der Makromolekülchemie, bei dem kleine Moleküle, sogenannte Monomere, sich zu langen Ketten, sogenannten Polymeren, verbinden. Diese Polymere weisen eine Vielzahl von Eigenschaften auf, die sie zu unverzichtbaren Materialien für verschiedene Anwendungen machen, von der Bauindustrie bis zur Elektronik.
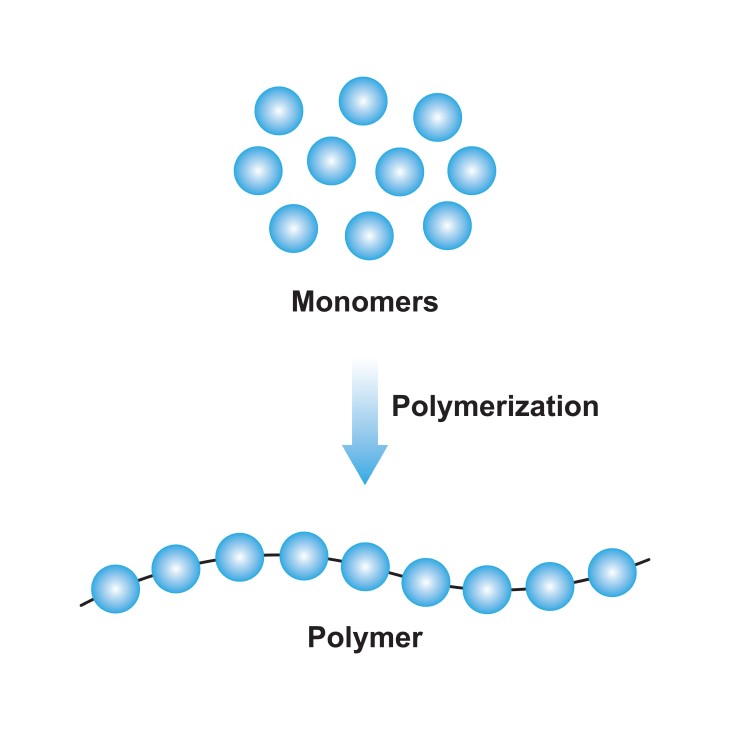
Traditionelle Polymerisationsmethoden beinhalten das Mischen von Monomeren und die Initiierung der Polymerisationsreaktion in einem separaten Behälter. In-situ-Polymerisation bietet jedoch einen einzigartigen Ansatz, indem Polymere direkt in einer Form synthetisiert werden, um ein geformtes Teil zu erhalten.
Die In-situ-Polymerisation ist die Initiierung und Ausbreitung einer Polymerisationsreaktion in einer spezifischen Umgebung. Der Prozess umfasst die Zugabe von Monomeren, Initiationsmitteln und anderen Reaktionskomponenten in eine Form, das Auslösen der Polymerisationsreaktion und das Zulassen des Wachstums und der Formung der Polymerketten innerhalb der vorgesehenen Struktur.
Diese direkte Integration der Polymerisation in die endgültige Anwendung schafft einen effizienteren und kostengünstigeren Ansatz für maßgeschneiderte Materialien mit optimierter Leistung für verschiedene Anwendungen.
Die In-situ-Polymerisation bietet mehrere Vorteile gegenüber traditionellen Polymerisationsmethoden, darunter:
- Maßgeschneiderte Eigenschaften: Die In-situ-Polymerisation ermöglicht die Bildung von Polymeren mit spezifischen Eigenschaften durch sorgfältige Auswahl der Monomere, Initiationsmittel und Katalysatoren. Der Prozess erreicht in der Regel auch hohe Molekulargewichte, was zu der Verarbeitung sehr starker und belastbarer Materialien führt.
- Leichtigkeit des Fließens
- Bildung komplexer Strukturen: Die In-situ-Polymerisation kann verwendet werden, um komplexe Strukturen zu erstellen.
Darüber hinaus hat die Vielseitigkeit der In-situ-Polymerisation zu einer Vielzahl von Anwendungen in verschiedenen Bereichen geführt:
- Automobilherstellung: Herstellung leichter und strapazierfähiger thermoplastischer Verbundwerkstoffkomponenten für Autoinnenräume, -außenbereiche und -strukturen
- Luft- und Raumfahrtfertigung
- Windkraft: Große thermoplastische Verbundwerkstoff-Rotorblätter
Nylon 6 formen
In diesem Fall schmilzt das Unternehmen Caprolactam-Monomere in einer Dosier- und Mischeinheit und fügt Additive bei einer Temperatur von etwa 100°C bis 120°C hinzu. Die Monomere werden dann in eine Form gepumpt, die auf 160°C eingestellt ist.
Sobald das Material in die Form gepumpt wird, wird die Polymerisationsreaktion aufgrund der erhöhten Temperatur der Form initiiert. Während der Produktion hat das Material etwa 16 Minuten Reaktionszeit. Dann wird der Deckel der Form angehoben, und das Teil wird in einen Ofen gebracht, wo es nachgehärtet wird.
Vor der Integration von sensXPERT Digital Mold war dieser Prozess äußerst stabil und erzeugte keinen Ausschuss. Die Zusammenarbeit des Unternehmens mit sensXPERT hat jedoch eine Gelegenheit aufgezeigt, die Produktionseffizienz zu steigern und gleichzeitig das Verhalten des Materials in der Form und die Qualitätsergebnisse zu überwachen.
Mehr über die sensXPERT Digital Mold-Lösung erfahren Sie hier.
Ergebnisse der Zusammenarbeit
Mit zwei Materialcharakterisierungssensoren, die in die Oberplatte der Form integriert sind, waren die Sensoren von sensXPERT ideal positioniert, um das Verhalten von PA6 zu überwachen und zu messen, während es in die Form gepumpt und zu polymerisieren begann.
Insgesamt analysierte sensXPERT 178 Produktionszyklen unterschiedlicher Länge, um Daten zu sammeln und ein maschinelles Lernmodell zu entwickeln. Nachdem alle Zyklusdaten gesammelt waren, führte das Datenwissenschaftsteam von sensXPERT eine multidimensionale Analyse durch, um eine Klassifizierung der verschiedenen überwachten Merkmale vorzunehmen – zum Beispiel wurden alle Teile, die nicht ausreichend fest für ihre anschließende Handhabung waren, zusammengefasst. Das Datenwissenschaftsteam begann dann mit dem Aufbau des maschinellen Lernmodells unter Verwendung eines Trainings-Test-Splits, wonach das resultierende Modell die Zyklen erfolgreich nach ihren Ergebnissen gruppierte.
sensXPERT stellte fest, dass eine Zykluszeit von bis zu 11 Minuten konsistent zur Herstellung ungeeigneter Teile führt. Zykluszeiten von 14 Minuten führten hingegen konsistent zur Produktion optimaler Teile. Daher konnte sensXPERT dem Unternehmen helfen, ihre Zykluszeiten um 12,5 % zu reduzieren.
Gesteigerte Produktionseffizienz und Qualitätsüberwachung
Durch die Messung des Materialverhaltens im Werkzeug und die Nutzung maßgeschneiderter maschineller Lernmodelle prognostiziert sensXPERT genau Prozessergebnisse. Dadurch ermöglicht es dynamische Anpassungen für höchste Qualität pro produziertem Teil.
Wie im Fall dieses Unternehmens unterstützt sensXPERTs Lösung für die Prozesskontrolle Hersteller dabei, Effizienz- und Optimierungsmöglichkeiten in der Produktion zu entdecken. sensXPERT erweitert auch die Möglichkeiten der Qualitätsüberwachung, indem es die Prozesse im Werkzeug transparent macht.
Insgesamt ermöglicht sensXPERT Herstellern, ihre Ausschussraten zu senken, Energieeinsparungen zu erhöhen und die Zykluszeiten für eine effizientere und kostengünstigere Produktion zu reduzieren.