How sensXPERT improves transparency in each molding cycle
Key Facts

A lack of process transparency hinders plastics manufacturers when it comes to ensuring part quality in their production. Limited insight on in-mold material behavior also leads to high and costly scrap.
Two companies that encapsulate high-voltage electrical components sought out sensXPERT in hopes of combatting these challenges. Whilst both companies use a reaction injection molding (RIM) process, one works with EPDM rubber and the other with epoxies.
Preliminary results in both cases illustrate that gaining transparency on in-mold material behavior leads to process stability. With access to this insight, manufacturers can implement adaptive process control and reliably produce in-spec parts.
Plastic processors, especially those working with thermoset materials, generally lack transparency as to what actually occurs in the mold during each processing cycle. Even processors who overmold a part with a thermoset protective layer face this challenge.
That makes it difficult to determine if the produced parts are in spec without conducting downstream quality assurance (QA) tests. Without little insight on the impact of in-mold material behavior on final part performance, molders struggle to control their processes and react to process drift in real-time. This can lead to exceedingly long cycle times, high energy usage, high scrap rates, and high cost of quality.
However, a new in-mold process monitoring system by NETZSCH Process Intelligence GmbH, namely The sensXPERT Digital Mold, offers real-time process transparency. By adopting machine learning (ML) algorithms, sensXPERT can accurately predict material behavior, which can then be used to aid manufacturers in dynamically controlling their processes and guaranteeing constant part quality. Correspondingly, sensXPERT supports molders in reducing cycle times, energy usage, scrap rates, and costs.
To illustrate sensXPERT’s value in addressing the abovementioned challenges, you will read about two comparable companies (Company A & Company B) working with NETZSCH to install its sensXPERT system. Both companies encapsulate high-voltage electrical components using a reaction injection molding (RIM) process. They differ in the polymers they use and the final parts they produce. However, they both face similar challenges with high scrap rates and high cost of quality owing to a lack of transparency during the molding process. This case study will highlight sensXPERT’s ability to increase transparency and improve processes, even before full technical integration of the system.
Material Insights & Common Challenges
Company A and Company B make functional parts in high-voltage applications like power grid solutions. More specifically, Company A produces connectors, while Company B produces bushings.
Using a RIM process, Company A overmolds ethylene propylene diene monomer (EPDM) rubber. This synthetic rubber is known for its durability, abrasion, tear resistance, excellent metal adhesion, and flexibility. Additionally, EPDM is resistant to most water-based chemicals, polar solvents, and solvents at elevated temperatures. Owing to a saturated backbone, EPDM provides excellent resistance to aging caused by heat exposure, UV radiation, weathering, and ozone. It can produce a very smooth molded surface. The material is especially suitable for electrical insulation due to its low electrical conductivity.
On the other hand, while Company B uses a RIM process, they differ in using epoxies to produce their parts. Epoxies are known for their excellent tensile, compressive, and flexural strength. They are also resistant to impact, abrasion, fatigue, high moisture and steam, broad chemical, radiation, and corrosion. Furthermore, the material has low post-cure shrinkage (1%) and a broad thermal performance (up to 190°C). Epoxies offer excellent adhesion to various fillers, reinforcements, and substrates. Similar to EPDM, epoxies also provide high electrical insulation. This facilitates their use in motors, generators, transformers, gear switches, bushings, insulators, printed circuit boards, pottants, and semiconductor encapsulants.
Regardless of the material difference, both companies face similar challenges in requiring more transparency during the RIM process. The lack of transparency makes it impossible for both companies to know whether they produce good or bad parts during each molding cycle. On that account, it becomes difficult to understand the correlation between material behavior during molding and the defects detected in a part during post-mold QA tests. In the cases at hand, a defective part is one that might fail to pass an electrical discharge or a high-voltage penetration test. An added concern is the ability to detect contamination of a material during processing.
Difficulties in transparency and post-processing QA can lead to high and costly scrap. To anticipate and reduce such scrap would improve manufacturing sustainability. The ultimate goal for both companies is to gain process transparency, improve process stability, boost quality, and reduce costs.

How Can sensXPERT Help?
The companies consulted the NETZSCH Process Intelligence team to see if its sensXPERT in-mold process monitoring system could improve quality control, reduce scrap, and better understand the effects of processing on final part performance. They also sought the sensXPERT technology to see whether the system could detect and reduce defects in completed parts. While the system does not directly track or measure defects, it does map out material behavior and transformation during cure. The resulting insight can help processors understand what occurs inside a mold, more quickly discover the cause of failures, and optimize their processes to account for material deviation, thus ensuring consistent quality outcomes.
The sensXPERT system includes specially designed and manufactured hardened dielectric sensors that are mounted in a mold at the very start of flow, near or at the gate, and at the end of flow. The system measures critical material and process parameters that occur in the mold during the entire molding cycle, including:
- Degree of Cure (DoC).
- Percent polymerization,
- Glass-transitions temperature (Tg),
- Viscosity and flow-front position,
- Temperature inside the mold, and
- Material deviations (e.g. those caused by aging, out-of-spec material, or in the presence of contaminants – such as when running recycled material or when metallic inserts are not fully cleaned of chips after machining).
The sensXPERT edge device, a hardened personal computer without a keyboard or monitor, sits outside the mold but very close to the press and is hardwired to the dielectric sensors. A WebApp that acts as the edge device’s interface empowers manufacturers to adjust their process parameters in real-time effectively. This interface visualizes running processes and, using predictive algorithms, provides operators with an optimal point of cure. The data on the edge device is transmitted to a customer’s account in the sensXPERT Cloud Service following a production cycle. In the Cloud, the data is parsed and compared with all previously collected data to evaluate specific quality indicators.
To help dynamically control processes and ensure part quality, historical data on the Cloud is used to train ML algorithms. The sensXPERT system can also take third-party sensor data – such as mold temperature, presssure, and humidity – into account, which can be integrated into the ML models as well. The trained and retrained algorithms are applied to the edge device so that the predictions of process outcomes are constantly refined. Based on the predictions, a technician can determine whether or not they should act and modify a process setting.
After fully installing the sensXPERT system, the companies can better understand whether pre-process material handling contributes to deviations during manufacturing. They will also gain more insight into how the curing mechanism affects final part properties and how that may contribute to failed post-process QA tests.
Preliminary Results
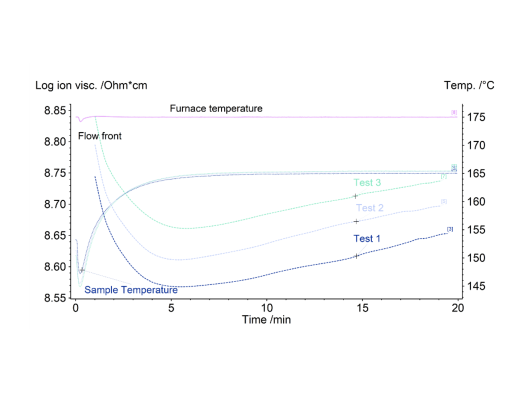
Based on laboratory characterization of EPDM rubber, the preliminary results above help explain what occurs during molding. As the material is heated, its viscosity lowers and flow increases, which is indicated by ion viscosity (in Ohm-cm). This represents the movement of the material. However, as the temperature continues to rise, crosslinking begins to occur. This increases viscosity and decreases the mobility of the ions, which suggests that flow is slowing. As follows, measuring a process parameter like ion viscosity can indicate the degree of cure and how the material fills the mold.
When the companies produce parts, further material characterization and encapsulation experiments will be conducted in an instrumented mold to test the hypothesis that the degree of cure is the critical property affecting whether or not encapsulated parts pass QA testing
What’s Next?
As depicted throughout this case study, processors that encapsulate high-voltage electrical applications in thermoset polymers are confronted by the lack of in-mold transparency during each molding cycle. They can achieve process stability only when they understand how material properties within the mold create deviations that lead to issues, such as scrap. Once they have in-mold transparency, they can reliably and repeatedly produce in-spec parts using adaptive process control without costly and time-consuming post-processing QA testing. At a time when manufacturers struggle to fill skilled positions, supply chain challenges and rising energy costs add pressure to the bottom line. Companies are also compelled to make their manufacturing footprint more sustainable. New ML-based tools, like The sensXPERT Digital Mold, can improve profitability and facilitate entering new markets and applications. sensXPERT’s technology can enable companies to maintain a digital thread of their processes and enhance in-mold transparency, cost control, and overall sustainable production.