"In collaboration with sensXPERT, ZF reinforced sustainability and efficiency in their molding process."
Rico Zeiler
Specialist in Process Engineering at ZF

Proven Success: Real-World Impact with sensXPERT
Discover how sensXPERT revolutionized manufacturing processes across various industries with our innovative solution. This page showcases a collection of real-world use cases that demonstrate the tangible benefits of our technology in action.
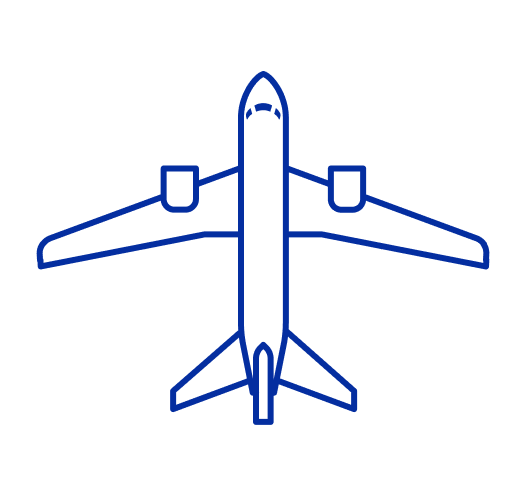
Aerospace Manufacturing
How an aerospace leader improved quality and efficiency with a cycle time reduction of up to 20%
Read Story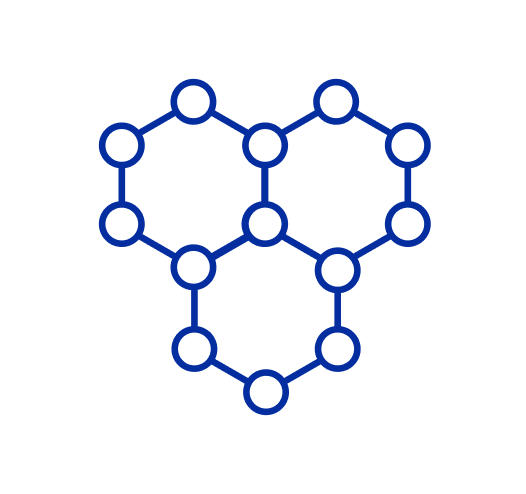
In-Situ PA6 Polymerization
sensXPERT Enabled the Company to Cut Down Their Cycle Times by 12.5%
Read Story
Back to the top