Real-Time Manufacturing Excellence Starts Here
sensXPERT Insight
Discover how sensXPERT transforms raw, real-time material data into precision-engineered decisions. With insights that reduce waste, optimize efficiency, and elevate product quality, we put you in control of your production process.
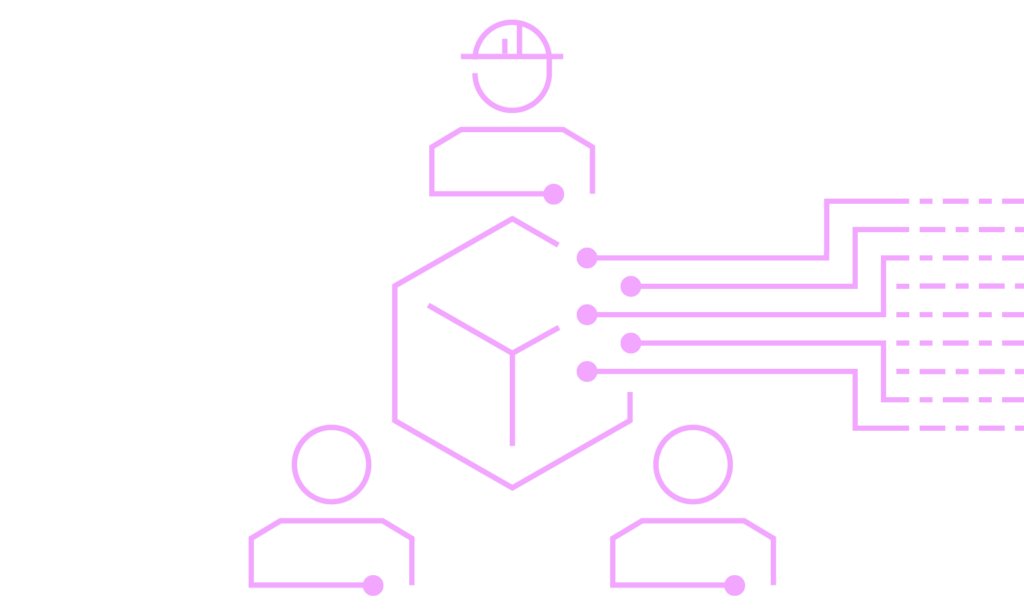
Why Top Manufacturers Choose sensXPERT Insight
Real-Time Monitoring
Gain instant insights into degree of cure, crystallization, glass transition temperature, and quality during every second of the production process.
Data-Driven Intelligence
Turn sensor and machine data into reliable insights that help you detect issues before they become problems.
Quality at Every Stage
Achieve unmatched consistency with reduced waste, fewer defects, and compliance with industry standards – all backed by sensXPERT’s process transparency.
How sensXPERT Insight Works
1
Capture Real-Time Material Data
Our cutting-edge dielectric sensors measure material properties including degree of cure, viscosity, glass transition temperature, crystallization, and more to provide unmatched visibility into your running process.
AI-Powered Data Processing
Our advanced AI algorithms identify patterns in your production data, ensuring any inconsistencies are flagged in real-time, long before they can impact product quality.
2
3
Deliver Insights You Can Trust
Turn complex data into simple, actionable insights. With sensXPERT, you’ll have the information needed to optimize efficiency, ensure compliance, and deliver top-tier quality.
Transforming Industries with Real-Time Process Insights
From aerospace to electronics, sensXPERT adapts to diverse industries and applications, ensuring quality and efficiency at every stage of production.
Aerospace
sensXPERT is an invaluable contributor to what our company aims to be, the leader in the aerospace industry.
Automotive
The sensXPERT technology allowed for more insight into material behavior throughout the molding process.
Machining
This AI-based technology perfectly supports our aspiration to further automate and digitize our value chain.
Leading the Future of Manufacturing Control
Conventional tools give you limited data. sensXPERT Insight gives you complete control.
With conventional tools, deviations go unnoticed until it’s too late. sensXPERT provides
real-time insights that empower you to act proactively, ensuring consistent quality and improved efficiency.
Temperature Sensor
Temperature sensors provide basic readings of heat levels within the mold. While they are useful for monitoring curing or molding processes, they only offer indirect insights into material behavior, leaving room for inconsistencies and quality issues.
Pressure Sensor
Pressure sensors measure force within the mold cavity, offering insights into material flow and compression. However, they cannot detect internal material states, such as cure progression, making them insufficient for ensuring complete process optimization.
sensXPERT Insight
sensXPERT Insight goes beyond traditional sensors by using dielectric sensor technology to monitor the molecular behavior of materials in real time. This enables precise control over cure, flow, and quality, ensuring consistent production outcomes and eliminating guesswork.