Is Plastics Manufacturing Sustainable?
The European Union has outlined its goals for a carbon-neutral society within the next 10 years, yet a major hurdle remains. The production of non-biodegradable materials is growing, and its industries are looking for more ways to tackle the ever-important objective: ‘net-zero’.

Plastics: A Growing Industry
The first fully synthesized plastic polymer to pioneer global attraction was Bakelite: a composite of non-natural compound resin mixed with fillers like wood and asbestos. It was invented in 1907 and sparked a consumer rush for the wonder material now coined ‘plastic’. Light, durable, and easily malleable, plastics manufacturing soon became a competitive industry.

Bakerlite: An Overview. Source: newsflicks
A substantial amount of plastic was created for use in WWII, with U.S. production rates increasing by 300%. Since 1950, it is estimated that global plastics production has amassed 9.2 billion tons and is set to rise by 34 billion tons in 2050.

Cumulative plastic waste generation and disposal (in million metric tons). Sourcwe: Science.org
The early 1960s saw a demand for next generation thermoplastics that could improve mechanical properties and thermal stability for high performance and engineering applications. Polymers such as polyether ether ketone (PEEK) became leading plastics for aerospace and nuclear industries, demonstrating unique singular properties for heat stability, tensile strength, and mechanical performance.
The market size for global high performance plastics is projected to grow to $42 billion by 2029. Engineering plastics also rose in prominence throughout the late twentieth century as a stable material for automotive interiors, electronics, and consumer products. In 2020, more than 22 million tons of engineering plastic was produced.
The plastics industry continues to grow exponentially. In 2021, the global market for plastics manufacturing was valued at $593 billion. This amount is expected to almost double by 2030.
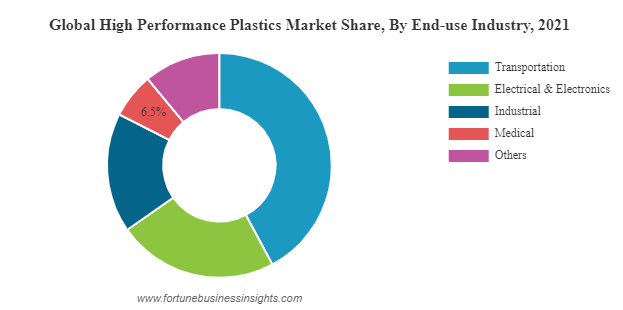
History of Climate Goals
Since the discovery of fossil fuels and their integral significance to industrialization, the planet has been at risk of pollution.
The United Nations Framework Convention on Climate Change (UNFCCC) was drafted in 1992, with the goals of recognizing catalysts to climate change and reducing greenhouse gases. During this time, general circulation climate models (GCMs) and integrated assessment models (IAMs) enabled scientists to assess ongoing impacts of emissions and prevention techniques. Early proposals from such findings leant to the discussion and popularization of nuclear power.
Carbon capture (CC) has become an important project since its initialization in 1996. The aim is to capture CO2 produced by industrial sectors and store it underground before it is released into the atmosphere. It has been accepted that carbon capture is critical to reaching the goal of zero carbon emissions by 2050, as set by the E.U.
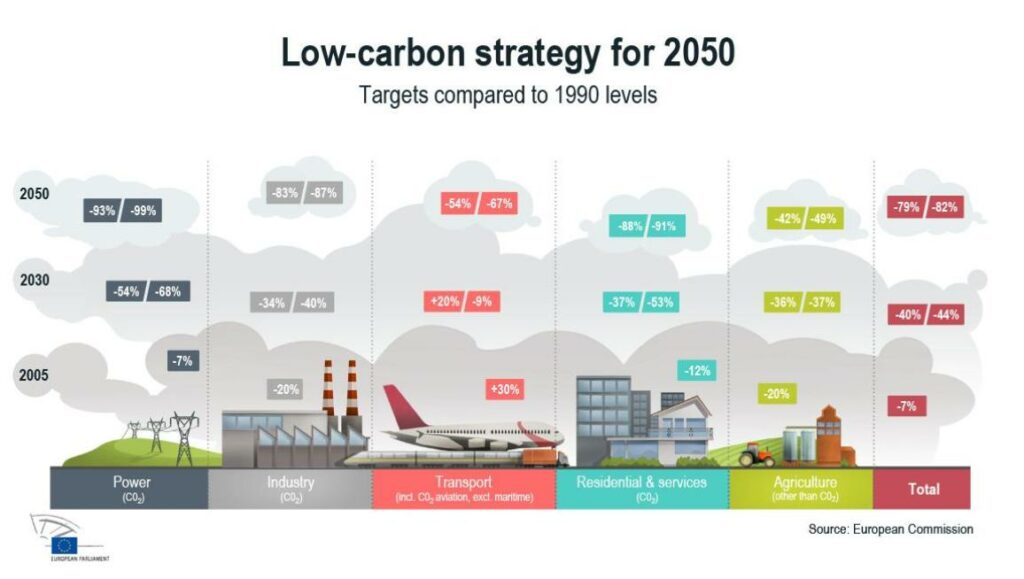
The Paris Agreement is the latest international effort to hold a legally binding treaty on actions taken against climate change. Adopted in 2016, 196 Parties at the UN Climate Change Conference (COP21) agreed to the goal of decreasing the global average temperature by 2oC. The treaty also aims to reduce greenhouse gas emissions by 43% before 2030.

Plastics and the Green Effort
The disposal of plastic waste is a great contributor to pollution, whether dumped in landfills and oceans or incinerated into the atmosphere. It was not until the late 1980s that recycling plastic started to occur. Up to 1990, the percentage for both incineration and recycling only increased by 0.7%. Additionally, by 2015 it was recorded that 55% of global plastic waste was still discarded, with only 20% recycled.

In 2022, the United Nations Environment Assembly (UNEA-5.2) came to a historic resolution, forging an international agreement that legally bound UN Member States to address the lifecycle of plastic pollution, from source to sea.
The European Green Deal
The European Green Deal is a strategy to deliver a modern, resource-efficient, and competitive economy. Announced back in 2019, the deal plans:
- To reduce net emissions of greenhouse gases to zero by 2050
- To decouple economic growth from resource use
- To leave no person or place behind in the transition
Key sectors, such as plastics manufacturing and supply, are to be provided with clean technology at an affordable rate to help reduce the carbon footprint of plastics production. This venture ensures the health and well-being of E.U. citizens, along with protecting, conserving, and enhancing natural capital biodiversity.

In addition to its goal of climate-neutrality, the Green Deal will improve energy efficiency within plastics manufacturing by 32.5% and increase the potential for renewable energy solutions by 32%. The Deal aims to accomplish these by 2030.
Simultaneously, the creation of a circular economy will help to reduce waste and reuse material where possible. With international collaboration, the E.U. can create a plan to make plastics manufacturing sustainable in a way that is inclusive, just, and more supportive for disadvantaged communities.
Taxonomy and Sustainable Solutions
To abide by the Green Deal, many communities could require investment towards achieving the aforementioned goals set out by the E.U.’s policies. With this, however, comes careful consideration to environmental, social and governance (ESG) factors.
Sustainable finance works in conjunction with the European Green Deal to highlight transparency in any risks associated with ESG factors, and those that could further impact the financial system. It also works to mitigate such risks with the correct governance of financial and corporate actors.

The sustainable finance strategy was published in 2021, proposing these actions:
- Extension of E.U. taxonomy framework and sustainable finance standards to recognize transition efforts
- Provision of tools and incentives to access transition finance
- The highlight of essential financial steps to become resilient to climate change risks
Nevertheless, without a clear framework these solutions cannot accurately support the target communities in plastics manufacturing.
Therefore, the E.U. taxonomy regulation is designed to create such a framework around the concept of sustainability that can precisely define a company’s operation, and whether or not it is environmentally friendly. The regulation defines a list of economic activities that can be considered sustainable. These are referred to as ‘taxonomy’.
There are six environmental objectives within the regulation:
- Climate protection
- Adaptation to climate change
- Sustainable use and protection of water and marine resources
- Transition to a circular economy
- Pollution prevention and control
- Protection and restoration of biodiversity and ecosystems
The E.U. taxonomy supports sustainable finance with a framework designed for safe investments in ensured financial products that abide by the regulation’s objectives.

sensXPERT Sustainable Solutions
sensXPERT provides high quality, real-time data in a single solution.
Effectually comprised of four elements: dielectric sensors, the sensXPERT Blue Box, sensXPERT Live, and the sensXPERT Hub, our sensXPERT Insight solution empowers plastics manufacturers from a variety of industrial sectors, including aerospace, transport, construction, and electronics packaging. Furthermore, this solution helps businesses reach their full potential through high-impact optimization opportunities that can benefit sustainable plastics manufacturing practices.
The latest process control solution by sensXPERT assists plastics processors by operating alongside molding solutions for rigid plastics or elastomers/rubbers, neat (unreinforced) polymers or composites, and with thermoplastic, thermoset, or vitrimer matrices. Its process data monitors moment-by-moment, in-mold materials and predicts evolving conditions both inside and outside of the mold, as well as how likely such conditions will affect end-use part performance.

This software allows for new levels of understanding and control over molding processes for plastics manufacturing. Quality assurance (QA) testing can be performed during the molding process so errors can be quickly recorded, and scrap reduced. Ultimately, sensXPERT achieves sustainable plastics manufacturing by lowering downstream production costs, shortening cycle times, reducing energy consumption, and removing unnecessary scrap.
The process control solution also provides the highest transparency required, with digital component tracking, for meeting the E.U. taxonomy regulation.
sensXPERT Insight
sensXPERT’s Equipment-as-a-Service solution provides real-time process control by understanding internal and external mold conditions. Dielectric sensors installed in manufacturing molds measure real-time material behavior using dielectric analysis, and a provided sensXPERT Blue Box, connected to the mold sensors, gathers the data. sensXPERT offers an interface to the Blue Box, namely sensXPERT Live, through which manufacturers can view and adjust their running production processes in real-time, as well as predict the optimal degree of cure/crystallization for production molding. The Blue Box also communicates all historical data to the sensXPERT Hub.
The Hub can visualize the historical process data from multiple machines, regardless of geographical location, providing total process transparency and data management that works in accordance with the E.U. taxonomy regulation, as well as supports businesses in ensuring financial investment.
Why Sustainable Plastics Manufacturing Matters
Solutions such as sensXPERT’s digital process control software can make a large impact on how plastics processors report on their sustainable practices. This is achieved through better documentation of CO2 use in relation to a company’s carbon footprint, as well as through accurate analyses of production cycles that can significantly cut energy and material waste.
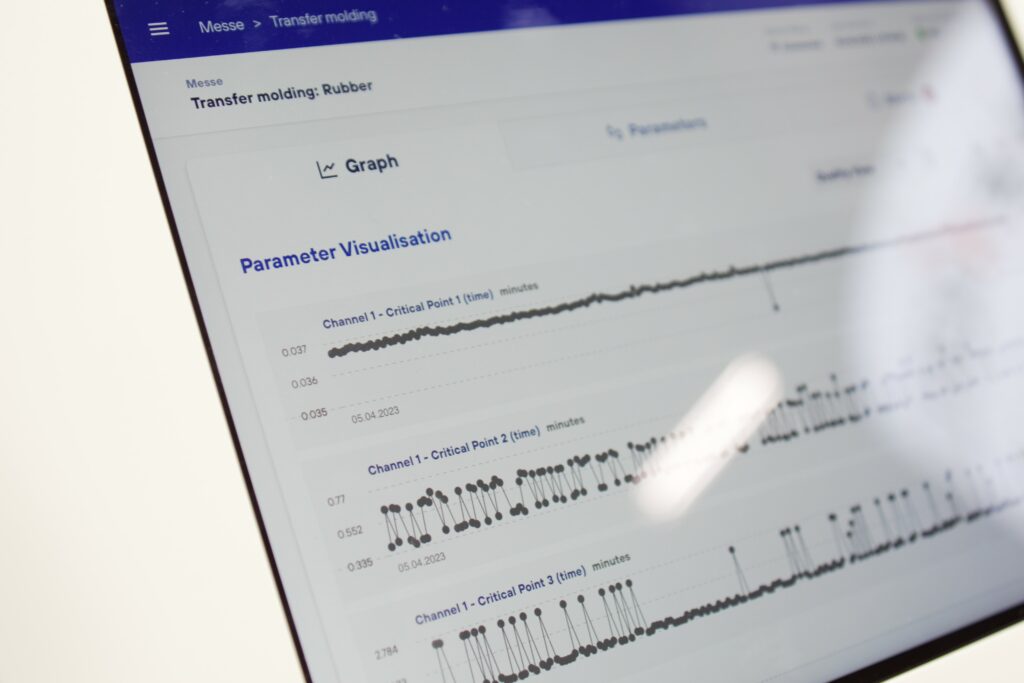
With the rate at which the plastics industry is continuing to grow, alongside the initiatives that are being implemented to track its effects on climate change and pollution, it is key for the industry to follow five steps on the path to turning plastics manufacturing sustainable:
- Ensure reporting on operations is thorough and consistent, abiding by the Sustainable Finance Strategy
- Implement process control solutions to gain accurate data and control over material behavior. Catch early production errors and save money on unsustainable scrap and material waste
- Employ industry 4.0 tool sensors and AI software with machine learning capabilities to boost efficiency in production
- Educate on rising materials such as thermosets and bioresins. Thermoset is growing in popularity and demand, as is the skills shortage for its operation
- Avoid missing process digitization and collaboration. Discover how different technologies and products can interact to improve process efficiency
Contact sensXPERT today and explore the technology that can save money for businesses and assist with E.U. taxation documentation. Together, the future for making plastics manufacturing sustainable looks bright.